Introduction
These notes relate to Hydrostatic drives / transmissions.
These are drives which include, as primary items, rotary hydraulic pumps and motors. ( Hydrostatic refers to the transfer
of energy using the pressure (head) of the flowing fluid, not from the kinetic energy of the flow). Strictly Hydrostatic drives can include
power transferred in a linear manner using hydraulic cylinders /pistons . The notes below relate only to rotary motion.
The units are coupled hydraulically to provide power transmission in static and in mobile applications.
It is possible to obtain hydrostatic drives with the pump and motor combined in one unit, with the necessary hydraulic piping
and components built in.
The hydrostatic drive has a major advantage compared to conventional geared systems in that the location of the driven component
is not constrained by the mechanical drive path which may include shafts, belts couplings gears, chains. The hydraulic motor
can be located at any position and orientation and is simply connected to the pump using pipes.
Hydrostatic drives enable smooth connection of the driven component from the driver eliminating the need for mechanical clutches. Use of variable displacement
pumps and/or motors enables the speed ratios to be very conveniently changed. Hydrostatic drives are, within their operating range, positive
drives and therefore the input power to drive the pump is directly related to the power requirements at the motor. The drive is similar
in performance to a mechanical drive system.
Hydrostatic drives can withstand continous stop/starting and reversing operations and are able to withstand shock loading.
Important note. When an hydrosttic drive is not operating there is no positive braking on the motors which can drift. It is therefore
often necessary to include mechanical braking on motors .
The following four drive arrangements are available using hydrostatic drives
1) Fixed Displacement pump and motor..This is equivalent to a fixed ratio machanical gearbox. This arrrangement has the clear
advantage compared to the gearbox
in that the hydraulic motor drive shaft can be very conveniently located.
2) Fixed Diplacement pump with variable displacement motor....This is equivalent to a multispeed gearbox. If the motor displacement is
arranged to be continuously varied this has a constant power characteristic with the torque available increasing as the speed is reduced..
3) Variable displacement pump with fixed displacement motor. At zero displacement the pump acts as a clutch. Continuously
increasing the pump displacement results in the motor speed under at approximately constant torque . This being limited by the maximum set pressure of the system or the power
of the pump driver.
4) Variable displacement pump and motor motor. This combination provides the most versatile arrangement of the availability of constant
torque and constant power. This option is clearly the most expensive to install and the most complicated to operate.
|
Two primary options are available for hydrostatic drives open circuit systems and closed circuit sytems
Open Circuit Systems
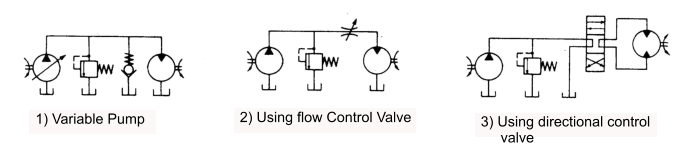 Open Circuit System Variations
In the open circuit option the pump draws fluid from a reservoir and the discharge from the motor is back to the reservoir. The ratio of
the pump displacement to the motor displacement is used to determine the speed ratio between the pump and the motor.
By using a variable displacement pump it is possible to adjust, dynamically, the drive ratio. The line from the pump to the motor
has to include a shuttle valve to ensure that cavitation does not occur in the event of the pump flow reducing while the motor over-runs
Closed Circuit Systems
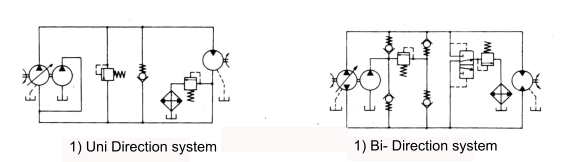 Closed Circuit System Variations
In an closed circuit variation the pump discharge is fed to the motor via control valves. The motor discharge returns to the
pump inlet. It is necessary in this option to include a small booster pump to ensure the the pump suction is is always at at positive pressure.
This option is generally used for vehicle drives when the advantage of dynamic braking is available. Dynamic braking occurs when the pump is slowed or stopped
the motor then starts to pump and drive the pump, which acts as a motor which is braked under the action of the prime mover.
For mobile, closed circuit , systems it is also necessary to include a cooler in the boosted pump suction feed to maintain the fluid temperature within
acceptable limits
Hydraulic Pumps
For Notes on positive displacement hydraulic pumps refer to webpage Positive displacement hydraulic pumps
Various types of positive displacement hydraulic pumps are available for use on hydrostatic drive systems . Below are links to notes relating to
a selection of the relevant pump types
The following linked notes are outline in nature and are provided to simply illustrate the working principals involved. For detailed
information it is recommended that the manufactureres literature is used.
Hydraulic Motors
For Notes on Hydraulic motors refer to webpage Hydraulic Motors
Various types of positive displacement hydraulic motors are available for use on hydrostatic drive systems .
Below are links to notes relating to a selection of the relevant motor types
Hydraulic motors are very similar to hydraulic pumps but with the operation reversed i.e instead of the shaft rotation resulting in the flow
of fluid as in pumps - In motors the fluid motion results in the shaft rotation. In principle a hydraulic pump can also be used
as a hydraulic motor.
However detailed design and operating factors often make this impractical.
|