Introduction
Mechanical seals are being used increasingly on fluid pumps to replace
packed glands and lip seals. Pumps with mechanical seals perform
more efficiently and generally perform more reliably for extended periods of time
Mechanical seals are provided to prevent pumped fluids from leaking out
along the drive shafts. The controlled leakage path is between two
flat surfaces associated with the rotating shaft and the housing respectively.
The leakage path gap varies as the faces are subject to varying external loads
which tend to move the faces relative to each other.
The mechanical seal requires a different shaft housing design arrangement compared to
that for the other type of seals because the seal is a more complicated arrangement
and the mechanical seal does not provide any support to the shaft.
In order for the mechanical seal to perform over an extended time period with
low friction the faces are generally hydrodynamically lubricated.
The fluid film will need to carry substantial load. If the load
becomes too high for the film surface contact will take place with consequent bearing failure. This lubricating film
is generally of the order of 3 micrometres thick , or less. This thickness is critical
to the required sealing function. Mechanical seals often have one face
of a suitable solid lubricant such that the seal can still operate for a period without
the fluid film.
Pressure Balance Seals
It is possible to reduce the seal contact pressure by using a pressure balanced
seal design of off-set a proportion of the force generated by the pumped fluid pressure.
This principle is illustrated in the sketch below.
Design Features
The mechanical seal generally includes three static seals.
- The sleeve seal - this is usually an O-Ring
- The seals between the moving seal member and the shaft or sleeve.- This is
often an o-ring but can be a wedge or vee seal. This seal may
not be used for bellows type mechanical seals
- The housing seal is generally an o-ring of a gasket.
|
All of these seal must be compatible with the fluid being contained and the
associated environment.
These seals may limit the design for high temperature applications.
In this case the bellows type alternative may be the best option.
The sealing faces are generally pressed together using some form of spring loading. Several
different spring loading systems are available.
- Single spring
- Multiple springs distributed around seal body
- Disc Springs
- Disc Springs
- Bellows
- Magnetic
|
For conventional mechanical seals the single spring arrangement is used.
The other spring arrangements are used if the space is restricted.
It is vitally important that the sealing surfaces are perfectly flat and are parallel.
The seal faces are usually dissimilar materials with the softer face being the narrower
surface. For abrasive applications similar hard materials are used e.g tungsten carbide.
The seal surfaces must have sufficient strength to withstand the hydrostatic fluid forces and must
be able to remove the heat generated by sliding action. Carbon is often used
against bronze, cast iron, stainless steel etc.
The seal surface must be flat, smooth and square to the shaft. Both surfaces
are normally lapped to a high quality finish. The harder surface is most
important because the softer surface is designed to run-in over the initial operating period.
The shaft design is critical. It must be rigid enough to support the seal in the
correct position and the shaft surface finish must be suitable to ensure good sealing on the
static seals (0.4 micrometers CLA or better). The shaft Total Indicated Runout (TIR) should
not exceed 0.125mm. There should be minimum shaft vibration. The
shaft may be subject to fretting corrosion as a result of micro-movements of the seal and is
is often desirable to have locally hardened surfaces or to use sleeves.
Assembly Options
There are a number of mechanical seal options
- External Seal..
This design is installed on the outside of the stuffing box with the sealed pressure
inside. This provides good access allowing the seal components to be be cleaned.
- Internal Seal..
Generally mechanical seals are mounted inside the stuffing box with the sealed pressure
outside the seal.
- Double Seals..
Mechanical seals mounted in pairs are used for sealing hazardous, toxic or abrasiv fluids and
are often provided with clean flushing fluid between the seals.
Double seals also provide an additional degree of safety were the pressure differentials
are likely to reverse and/or there is a high risk of the sealing failing. There are a number
of double seal assembly options as listed below.
- In Series - Used primarily to overcome the risk of failure of a single seal.
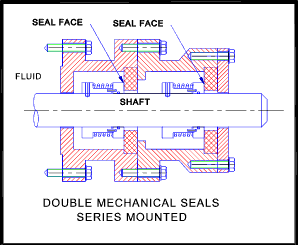
- Face to Face - Used when a cooling fluid interface is required . One seal is used for the process
fluid the other seal is used for the coolant.
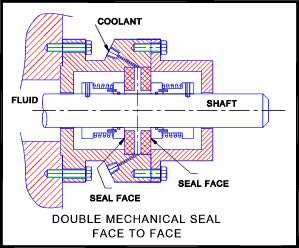
- Back to Back - Used when an abrasive fluid is being contained and both seals are flushed with a clean buffer fluid.
The flushing fluid is introduced at a higher pressure the process fluid
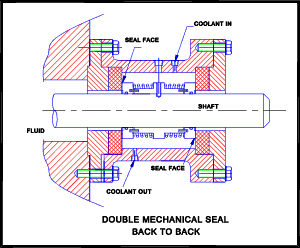
|
The are a large number of variant mechanical seals e.g split seals. Improved systems are constantly
being introduced onto the market
Additional Equipment
The use of mechanical seals generally involve the use of additional equipment primarily for
the flushing /coolant systems. This includes pumps, coolers, strainers, filters etc.
|