Introduction
The harmonic gear allows high reduction ratios with concentric shafts and
with very low backlash and vibration. It is based on a very simple construction utilising
metals elasto-mechanical property.
Harmonic drive transmissions are noted for their ability to reduce backlash in a
motion control system. The principle of operation of harmonic gears is through the use of a thin-walled
flexible cup with external splines on its lip,placed inside a circular thick-walled
rigid ring machined with internal splines. The external flexible spline
has two fewer teeth than the internal circular spline. An elliptical
cam enclosed in an antifriction ball bearing assembly is mounted inside the flexible
cup and forces the flexible cup splines to push deeply into the rigid ring at two opposite points
while rotating. The two contact points rotate at a speed governed be the difference in
the number of teeth on the two splines This method basically preloads the teeth, which reduces backlash.
Harmonic Drive Limitations
Harmonic drives have speed reductions single stage of 30:1 to 350:1. The lower ratios
are limited because of fatigue considerations on the flexispline member.
The harmonic drive is normally not suitable
for high power levels above 6kW ..
A typical large duty Harmonic drive will have dimensions of about 280mm dia x 150 mm long and will be able to
continuously transmit an output torque of 2270 Nm at an output speed of 20 RPM and
and input speed of 2000RPM (4.7 kW output)- This unit will be able to transfer higher
torques for short time durations e.g a momentary torque 9000Nm. The efficiency would be
about 70%. This unit would weigh about
42 kg. ..... A worm drive for a similar drive (1800 RPM imput speed ,70-1 reduction same
output torque )would weigh 327 kg and would be in a case about
750mm high x 360mm wide x 500mm wide..Surprisingly for this duty the efficiency of the
worm unit would be 77%
Harmonic Drive Applications
- Robotics
Harmonic Drives offer robot manufacturers many benefits
including zero backlash, high positional accuracy, low vibration and
a compact design. They can be used in any of the robot axes
and their light weight design contributes minimal weight to the robotic arm
which increases robot payload capacity.
- Machine Tools
Harmonic drives allow accurate control of the motions for axis positioning and for
tool changing. >
- Medical
Applications using harmonic drives include patient beds, rehabilitation equipment,
and MRI / Cat scan gantries.
- Military Aerospace
The Harmonic Drives are used to accurately rotate and tilt the antennas and arrays.
They are also used for driving lunar vehicle motions and positioning aerials and telescopes e.g.
Harmonic drives are used in the Hubble Telescope.
|
Harmonic Gear construction
Wave Generator: The wave generator is an oval-shaped cam with a thin ball
bearing placed around the outer circumference of the oval cam. The wave generator is mounted onto the motor shaft.
Flex Spline: The flex spline is a thin, cup-shaped component made of elastic
metal, with teeth formed along the outer circumference of the cup's opening.
The gear's output shaft is attached to the bottom of the flex spline.
Circular Spline:
The circular spline is a rigid internal gear with teeth formed along its
inner circumference. These teeth are the same size as those of the flex spline, but the circular spline has two more teeth than the flex spline. The circular spline is attached to the gearbox along its outer circumference.
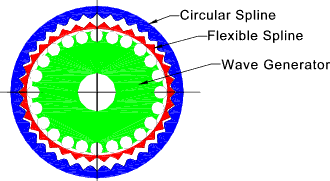
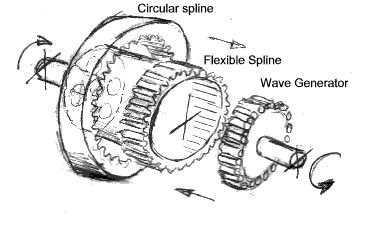
Harmonic Gear Operation
The wave generator is mounted on the drive shaft and as it is rotated it imparts a
continuously moving elliptical form or wave-like motion to the Flexspline. This causes
the meshing of the external teeth of the Flexspline with the internal teeth of the
Circular Spline at their two equidistant points of engagement to progress in a
continuous rolling fashion. It also allows for full tooth disengagement
at the two points opposite the minor axis of the Wave Generator.
Since the Flexspline has two less teeth than the Circular Spline and because
full teeth disengagement is made possible by the elliptical shape of the Wave
Generator, each complete revolution of the Wave Generator causes a two tooth
displacement of the Flexspline in relation to the Circular Spline.
This displacement is always in the opposite direction of the rotation of the
Wave Generator (see diagram)e.g if the Wave Generator is rotating in a CW
direction, the two-tooth-per-revolution displacement of the Flexspline will be
in a CCW direction and vice versa
In this way, a basic three element
harmonic drive component set is capable of functioning as a speed reducer.
Input from a main power source through the Wave Generator is at a high speed, but
the two-tooth-per-revolution displacement causes the Flexspline, which is the output
element, to rotate in the opposite direction of, and at a considerably slower
speed than, the Wave Generator. The reduction ratio which results can
be calculated by dividing the number of teeth on the Flexspline by two
(the difference between the number of teeth on the Circular Spline and
the Flexspline). If a fixed Circular Spline had 80 teeth and an
output Flexspline has 78 teeth, the ratio would be 80/(80-78)=40:1
Harmonic Drive characteristics
- High speed reduction ratio:
A Harmonic Drive has high single-stage coaxial reduction ratios of 1/30 to 1/320 using
a very simple three part mechanism.
- Free of backlash (lost motion):
Different from the ordinary tooth-with-tooth mating mechanism, the
Harmonic Drive can be made with very little -- nearly zero -- backlash.
- High precision:
With the Harmonic Drive, high positional/rotational accuracy is possible
because a number of teeth are mating at the same time and the 50% of the teeth are mating
at 180o symmetrical with the other 50% of the mating gears.
as a result pitch errors and accumulated pitch
errors on rotational accuracy are neutralised to ensure improved
positional/rotational accuracy.
- Small numbers of components and ease of assembly:
Because it comprises high reduction ratios are available with only three basic
components and since all three components are co-axially
aligned, the Harmonic Drive can be easily built into component-assembled
products.
- Small-sized and lightweight:
Machinery/equipment can be made smaller in size and lighter in weight because the
Harmonic Drive provides similar levels of torque and speed reduction
ratios as conventional gearing mechanisms at 30% the size of conventional
products of similar capacity and at less than 50% the weight.
- High torque capacity:
The flexspline is made of special steel with a higher resistance to fatigue.
Different from the typical driving force transmission
apparatus, every tooth is subjected to very little force but provides a
high capacity of torque. This is because up to 30% of the teeth are always taking some load
and these teeth come into contact with one another face to
face. Therefore every tooth is subjected to a minimum of force while providing a
maximum of torque.
- High efficiency:
The mating portion of each tooth is subjected to very
little slide motion. Therefore, motion loss due to friction is
reduced substantially. This is why the Harmonic Drive can maintain a
high level of efficiency, allowing for the down sizing of driving
motors as a result.
- Quiet, vibration-free operation:
With the Harmonic Drive, quiet and vibration-free operations are possible
because the teeth do not come into rolling contact with one another,
and since the circumferential speed of each tooth is low, the
teeth provide a well-balanced force.
|
|