Gear Selection Options
When a drive application requires rotary motion to be transferred with speed change
and or torque change a number of options are available controlled by system layout, economics and power capacity.
The drive transmission selection is selected from the options below in order of convenience.
When a drive application requires rotary motion to be transferred with speed change
and or torque change a number of options are available controlled by system layout, economics and power capacity.
The drive transmission selection is selected from the options below in order of convenience.
- Belt Drive ( flat, vee , synchronous )
- Chain drive
- Gearbox - geared motor
- Purchased Stock gears- unlubricated(Plastic/metal- plastic/plastic )
- Purchased Stock gears- metal lubricated
- Engineered gears
|
It must be emphasised that designing and manufacturing a gear system is relatively, expensive
and inconvenient if a proprietory system is available which will do the job..
The notes on this website enable initial basic gear design to be conveniently carried out. I do recommend that for
detail design of gears the relevant standards should be used and/or high quality reference document should be used. A very good , but expensive book
is "Handbook of Practical Gear Design " by Stephen P. Radzevich and D. Dudley ref.
Handbook of Practical Gear Design (Mechanical Engineering (CRC Press Hardcover))
Another convenient method of designing gears to the codes is to use the excel spreadsheet based system of
calculating programmes ref
Mitcalc.com -Gear calculations .
Gear Forming Notes
The performance, life , vibration and noise levels of a gear set is directly related to the machining process ,
heat treatment, and finishing of gear teeth. Notes on the production/forming /finishing of gear
teeth are found at Gear Forming
Types Of Gears
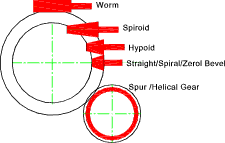
Note: More details and pictures of all gear types below are to be found at the links below table
Type |
Notes |
Further Notes |
Spur |
Majority of gears are spur. Relatively easy to design
and make. Parallel shafts. High efficiency (99% per train).
No side thrust. Can back drive. Single Ratio up to 1:10.
Can be made very accurate with low vibration /noise.
Normally steel pinions require lubrication. Plastic gears can be
used requiring no lubrication |
Spur Gears |
Internal Spur |
Similar performance to normal spur. Results in compact drive geometry. Used in manufacture of epicyclic / planetary gears. |
Helical |
Single Helical have similar properties to spur. However drive results in axial thrust. Gears are smoother/quieter for the same size/spec. The gears can run at high speeds up to large diameters. Higher torque/life capabilities for same size as spur. |
Helical Gears |
Double-Helical |
Similar benefits to single helical but with no generated side thrust. Higher performance compared to single helical |
Crossed-Helical |
Shaft at 90o. Difficult to make accurately. Smooth drive. |
Worm |
Offset shafts at 90o. Very high ratios possible in single stage. Sliding action. One gear is normally copper allow (bronze). Low efficiency at higher ratios and low speeds. Lubrication essential for mechanical and thermal reasons. Cannot backdrive at high ratios. |
Worm Gears |
Bevel Gear |
Mainly used for drive transmission through 90o.
Only low ratios used (4:1 and less). Lubrication required. Some vibration on spur type: Helical type smoother. |
Bevel Gears |
Spiroid |
Perform a similar function to worm boxes but the gears have characteristics which combine those of the bevel and worm gears. High powers and speed ratios are possible and mechanical efficiencies higher than worm boxes for equivalent ratios. |
|
Harmonic Drive |
Performance advantages include high-torque capacity, concentric geometry, lightweight and compact design, zero backlash, high efficiency, high ratios (up to 320:1), and back drivability. Harmonic drive systems suffer however, from high flexibility, resonance vibration. Used in robotics |
Harmonic Drives |
Brief Comparison
Type | Normal Ratio Range | Pitch Line Velocity (m/s) | Efficiency Range |
Spur | 1:1 to 6:1 | 25 | 98-99% |
Helical | 1:1 to 10:1 | 50 | 98-99% |
Double Helical | 1:1 to 15:1 | 150 | 98-99% |
Bevel | 1:1 to 4:1 | 20 | 98-99% |
Worm | 5:1 to 75:1 | 30 | 20-98% |
Crossed Helical | 1:1 to 6:1 | 30 | 70-98% |
Additional Notes on Gear Efficiency
Gear Box Notes
|