Drilling Process
The drilling machine (drill press) is a single purpose machine for the production
of holes. Drilling is generally the best method of producing holes. The drill is
a cylinderical bar with helical flutes and radial cutting edges at one end. The drilling operation
simply consist of rotating the drill and feeding it into the workpiece being drilled.
The process is simple and reasonably accurate and the drill is easily controlled both in cutting
speed and feed rate. The drill is probably one of the original machining processes and is the
most widely used.
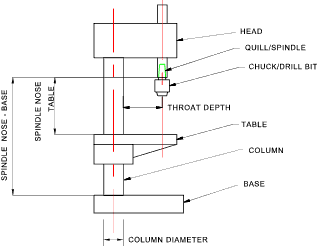 Drilling machine -important features/dimensions
Notes on Selection of Drilling Machines
Normal pillar drilling machines (Drill Press) are specified basically by the size of hole
the machine can drill in Mild Steel i.e a 16mm machine can drill holes upto and including 16mm dia in mild steel.
The speed range of a drilling machine is related to the size e.g. machines for small holes down to 1mm
can have speed ranges up to 8000rpm. Larger drilling machines more suited for drilling holes.
up to 25mm will have a more limited range. A machine which is used to drill
larger holes ( >15mm) is not generally suitable for drilling small diameter holes (< 1 mm). Smaller machines
are provided with permanent chucks whilst larger machines gnerally include morse tapers for
fixing the drills.
Most pillar drills are manually fed using a rotating lever driving
the vertical motion of the spindle. Larger machines can have power drives feeds.
A belt driven spindle is often a convenient low cost option but there is a tendency
in modern times to use geared /inverter drives.
When drilling holes in a material a number of factors should be considered including
- Material being drilled
- Hole size
- Hole quality.
- Speed /Feed required
- Depth of hole
- Through or Blind Hole
- Need for coolant
- Capacity of drilling machine
- Method of work holding. Hand held, vice, clamped
- Orientation of drill (horizontal , vertical drilling, angle
- Swarf control
|
Drilling Machines/ Machining Centres
The machines below are the classical designs. The modern trend is towards machining
centres which are CNC controlled machines with tool changing facilities and ability to perform multiple
machining operations including drilling.
Notes on Selection of Drilling Machines
Bench Drill
The most common form of drilling machine is the bench drill. As the name implies
this machine is normally bolted down to a bench. The workpiece can be clamped onto the
worktable or onto the base. Tee slots are normally provided for this function.  The worktable can be
moved up and down the vertical column.  The worktable can be clamped at the selected height.  The drill is normally located in a three jaw chuck which is rotated
by the drive system. The figure below shows a belt drive.  Modern bench drills are driven by more sophisticated
arrangements.  The chuck is moved up and down by a feed handle which drives rotating spindle via a rack
and pinion mechanism.
Pillar Drill
The pillar drill has the same features as the bench drill. This drill is
however free standing and is of a far heavier construction able to take larger drills. The larger drills
normally have taper shanks which are located within a taper bore in the spindle end. These tapers
are standardised as morse tapers.
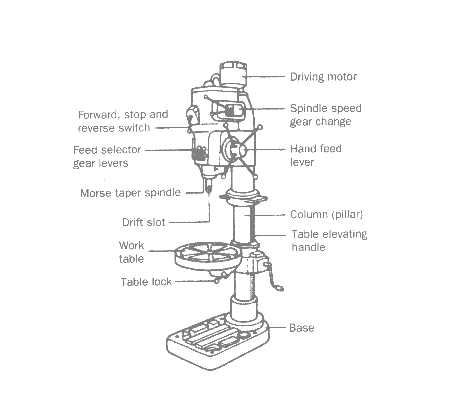
Radial Arm Drill
The radial drill is a free standing and the workpiece is clamped in position on the base.
The drill head is positioned using motorised drives.
Drills
There are two common types of twist drills, high-speed steel drills, and carbide-tipped drills.
The most common type used for normal workshop practice is the high-speed steel twist drill
because of its low cost. Carbide-tipped metal drills are used in production work where
the drill must remain sharp for extended periods, such as in a numerically
controlled drilling machine. Other types of drills available include solid carbide
drills, TiN coated drills, diamond drills etc. etc.
Twist drills shanks are either straight shank or tapered shank (Morse taper). Straight shank
twist drills are usually 12mm or smaller and are gripped in the drill chucks.
Tapered shank drills are usually for the larger drills that need more strength which
is provided by the taper socket chucks.
Common twist drill sizes range from 0.3mm to 90mm in diameter. Larger holes are cut by special drills that
are not considered as twist drills.
Types of Drills Bits
Typical Drilling Processes
Drilling Feeds and Speeds
The notes below ralate to HSS drills. For drills manufactured with more exotic material
combinations much higher feed and speed rates are viable
Drilling feeds range from 0,03m to 0,5mm rev the feed rate being higher as the drill size
increases from say 1mm to 60mm.
Table of drilling speeds
Material |
Drilling speed |
m/min |
Aluminium /alloys |
35-65 |
Brass /Bronze |
35-75 |
Copper |
30-60 |
Malleable iron |
20-40 |
Grey Cast iron |
24-30 |
Nickel/Monel alloys |
12-20 |
Nimonic alloys |
6-9 |
Mild Steel |
20-30 |
Alloy Steel |
12-18 |
Medium Carbon Steel |
14-20 |
High Tensile Steel |
5-14 |
Stainless Steel |
6-15 |
Aus. Stainless Steel |
6-10 |
Mart. Stainless Steel |
12-20 |
Zinc Based alloy |
45-75 |
Tapping /Clearance drill sizes
The tapping sizes are based on BS 1157:1975 and the clearance sizes are based on BS 4186:1967
Dia (Pitch) |
Tapping Drill size |
Clearance Drill Size |
Close (H12) |
Med (H13) |
Free (H14) |
mm |
mm |
mm |
mm |
mm |
1,6(0,35 |
1,2 |
1,7 |
1,8 |
2,0 |
2,0 (0,40) |
1,6 |
2,2 |
2,4 |
2,6 |
2,5 (0,45) |
2,05 |
2,7 |
2,9 |
3,1 |
3,0 (0,50) |
2,50 |
3,2 |
3,4 |
3,6 |
3,5 (0,60) |
2,90 |
3,75 |
3,95 |
4,2 |
4,0 (0,70) |
3,30 |
4,3 |
4,5 |
4,8 |
5,0 (0,80) |
4,20 |
5,3 |
5,5 |
5,8 |
6,0 (1,0) |
5.00 |
6,4 |
6,6 |
7,0 |
8,0 (1,25) |
6.80 |
8,4 |
9,0 |
10,0 |
10,0 (1,50) |
8,50 |
10,5 |
11,0 |
12,0 |
12,0 (1,75) |
10,20 |
13,0 |
14,0 |
15,0 |
14,0 (2,0) |
12,00 |
15,0 |
16,0 |
17,0 |
16,0 (2,0) |
14,00 |
17,0 |
18,0 |
19,0 |
20,0 (2,50) |
17,50 |
21,0 |
22,0 |
24,0 |
24,0 (3,0) |
21,00 |
25,0 |
26,0 |
28,0 |
30,0 (3,5) |
26,50 |
31,0 |
33,0 |
35,0 |
36,0 (4,0) |
32,00 |
37,0 |
39,0 |
42,0 |
42,0 (4,50 |
37,50 |
43,0 |
45,0 |
48,0 |
48,0 (5,0) |
43,00 |
50,0 |
52,0 |
56,0 |
56,0 (5,5) |
50,5 |
58,0 |
62,0 |
66,0 |
64,0 (6,0) |
58,0 |
66,0 |
70,0 |
74,0 |
72,0 (6,0) |
66,0 |
74,0 |
78,0 |
82,0 |
|