Introduction
Cast Irons are a family of ferrous metals with a wide range of properties produced by
being cast into shape as opposed by being formed. Cast Irons contain 2% to 4% Carbon and
1% to 3% Silicon. Other elements are used to control specific properties.
Cast irons have a wide range of mechanical properties which make them suitable for use
in engineering components. The wide spread use of cast
iron is as a result of its low cost and versatile properties.
A iron-carbon liquid containing over 2% C cooled very slowly will result in a graphite
(pure carbon) and iron crystallising out to form cast iron. In the practice
at normal cooling rates the metastable cementite Fe 3C is formed.
High carbon content metals can, under controlled conditions, solidify as stable
iron-graphite systems or metastable iron-carbide systems. Rapid cooling
discourages the nucleation graphite and encourages the formation of metastable iron
carbide. Longer holding times at higher temperatures and slower cooling
and the addition of certain alloying elements encourage the formation of stable
iron-graphite phase.
Cast iron contains significant amounts of silicon in addition to the high carbon
content. Cast irons are therefore really iron-carbon-silicon alloys.
The presence of silicon in iron carbon alloys promotes the formation of graphite.
The true (equilibrium /stable ) phase diagram for iron-carbon is similar to the metastable one
on the carbon steel page ( Phase diagram )
. The phase diagrams for
iron-carbon-silicon is similar but the eutectic/eutectoid points are moved to the left. A diagram for
one containing 2% silicon is shown below.
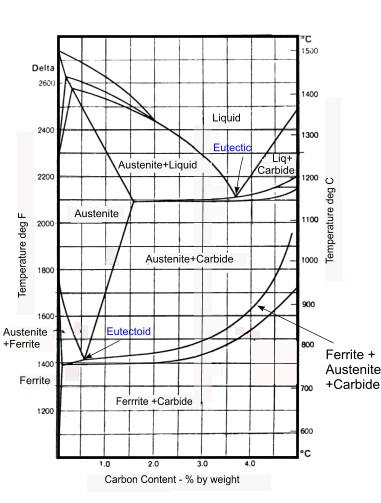
Cast Iron Production
Cast Iron production is relatively unsophisticated. It mostly involves remelting
charges consisting of pig iron, steel scrap, foundry scrap, and ferro-alloys to give
the appropriate composition. The cupola, which resembles a small blast furnace, is
the most common melting unit. Cold pig iron and scrap are charged from
the top ontoa bed of hot coke through which air is blown. Alternatively,
a metallic charge is melted in a coreless induction furnace or in a small
electric-arc furnace. The resulting types of cast iron are described
below;
Grey Cast Iron
Standard..Standard..BS EN 1561:1997 : Founding. Grey cast irons ... UTS 170-370 MPa, Elongation- 0,5-0,8%
Has ferrite and graphite (or pearlite and graphite) structure. The graphite can exist as flakes or spheres....
Grey cast iron is the most widely used of all cast irons and engineers often simply refer
to grey cast iron as cast iron. Grey cast iron contains 2,5%-4% carbon
and > 2% silicon. The silicon encourages formation of graphite from the
unstable cementite. The graphite is in the form of irregular flakes
which show up when the metal is fractured as the identifiable grey matrix.
Because of the presence of graphite cast iron is brittle unless it is specially
treated.
Grey cast iron is highly dependent on the rate of cooling of the
casting and of the section thickness. Thin sections can have reasonable
tensile strength which is not maintained as the section thickness is increased. The properties of
the grey cast iron is very dependent on the proportions of graphite in the matrix.
If all of the carbon has separated from the molten metal (full graphitisation)
then the grey cast iron resulting will have graphite flakes in a ferritic matrix.
If however 0,5% to 0,8%of the carbon remains in the form of Fe 3C the the
resulting grey cast iron matrix will be pearlitic and the cast iron will be stronger
and harder.
Sulfur is present in cast iron and generally is is kept low .
Manganese is often present and combines with the sulfur as a precipitate. Both
elements on their own restrict the formation of graphite.
The mechanical
properties of grey cast iron result from the effects of chemical composition and the
cooling history. In general as the combined equivalent of carbon and silicon
is reduced the strength of the cast iron is increased. When tensile strengths
above 350MPa are required, for thicker sections, alloying additions of chromium, nickel
or molybdenum are required.
Wear Resistance
Grey cast iron has outstanding resistance to sliding friction wear and has been used very
successfully,throughout the twentieth century,for sliding surfaces including cylinder bores, piston rings
and slideways on machine tools. Because of the effect of the graphite flakes
grey cast iron has and excellent resistance to galling and seizing and has a low coefficient
of friction.
Machinability
Grey cast iron is one of the easiest iron alloys to machine. The ferrite-graphite
cast iron is the easiest the fine pearlite matrix cast iron is more difficult.
Damping Capacity
Grey cast irons have an excellent capacity for absorbing vibration energy and thus damping
vibrations. This property is most evidenced with a high percentage of graphite flakes.
White Cast Iron
Standard..BS EN 1562:1997: Founding. Malleable cast irons ...
UTS 600-800 MPa, Elongation 2-3%...
Has a structure of pearlite in a cementite matrix making it hard, brittle and difficult
if not impossible to machine. It has limited applications in industry, it is
used for wear resisting components such as extrusion dies and cement mixer
liners. Fracture surfaces have light-coloured appearance.
Malleable Cast Iron..
Standard..BS EN 1562:1997: Founding. Malleable cast irons
Heat treated forms of white CI to improve ductility while maintaining the benefits of
of high tensile strength ;
The greatest use of white cast iron is for the manufacture of malleable cast iron.
This is produced by heating white cast iron at a temperature of 870oC for an
extended time period and then cooling at a slow controlled rate. The
cementite loses carbon which forms into free nodules. The final product is a
ferrite matrix with include free nodules of carbon. Malleable cast
iron has superior mechanical properties compared to grey cast iron apart from wear.
Increased strength and wear resistance with reduced ductility are obtained by
converting the structure to carbon nodules in a pearlitic matrix (or tempered martensitic). This involves heating
the malleable cast iron to a temperature of 970oC for over 12 hours and
then air cooling it. The faster cooling in air produces less ferrite and
a finer pearlic structure. A martensitic matrix structure results if the
cast iron is heated to a slightly lower temperature (about 940oC) and then
quenching it in oil.
Malleable iron castings are produced in section thicknesses ranging from about
1,5 to 100 mm and in weights from less than 0,03 to 180 kg or more
The three principle types of malleable cast iron available are ;
-
Whiteheart..UTS 250-400 MPa, Elongation 4-10%...
This is heat treated white iron compound producing an outer ferrite layer
and a ferrite/pearlite core Easy to cast in thin sections, which have a tough core....
-
Blackheart...UTS 290-340 MPa, Elongation 6-12%... Soaked at high temperature to cause the cementite to break down, then slowly
cooled to give ferrite and graphite
-
Pearlite... UTS=450-550 MPa, Elongation 6-12%... Similar to blackheart but faster cooling to produce a pearlite structure
with higher strength
|
Malleable iron is preferred over ductile iron for thin-section castings and for components as listed below:
- Components that are to be pierced, coined, or cold formed
- Components parts requiring maximum machinability
- Components that must retain good impact resistance at low temperatures
- Components requiring wear resistance (martensitic malleable iron )
|
Nodular Ferritic (Ductile Iron)
Standard..BS EN 1563:1997 : Founding. Spheroidal graphite cast iron
... UTS 350-480 MPa, Elongation-6-16%...
Nodular Cast Iron is obtained by adding magnesium just before casting. This
encourages the graphite to form spheres or nodules.
Ductile iron consists of graphite spheroids in a matrix of ferrite, pearlite or both. The graphite spheroids
provide some much improved mechanical advantages compared to the graphite flakes in grey cast iron.
Ductile cast iron is similar to grey cast iron in having a low melting point, good fluidity, castability,
excellent machinability and wear resistance. However compared to grey cast iron it has improved strength, ductility
toughness and hot workability.
Ductile iron as found wide acceptance and competes favourably with steel such that its
use in engineering has increased in recent times as while grey cast iron and malleable
cast iron has fallen in popularity as other materials such as plastics have found favour.
Ductile iron has a clear advantage over malleable iron for applications where low
solidification shrinkage is needed or where the section is too thick
to permit uniform solidification as white iron (Solidification as white iron throughout
a section is essential to the production of malleable iron).
|