Introduction
Generally heat lost from a hot or warm system system to the surroundings is waste and has a direct
effect on the efficiency of the system. Also for systems which are
operated as cold systems, heat gained from
the surroundings reduces the efficiency of the cooling process.
Typical hot systems include.
House Central heating systems
Turbine Plants
The human body in a cold environment
Steam transfer piping
Heat exchangers
Furnaces
Typical cold systems include.
Refrigerators and Freezers
Cryogenic Plants
The human body in a hot environment
In all these cases heat is transferred by conduction to (or from) the outer surfaces and
then it is mainly transferred by convection and radiation to (or from) the environment. These losses
are reduced by thermal insulation. The primary requirement of thermal
insulation is that it has a low thermal conductivity. Typical insulating materials include
glass fibre, rockwool, magnesia, diatomaceous earth, polystyrene, wool, wood fibres etc.etc.
There are hazards involved in the use and application of thermal insulation. Asbestos has excellent
thermal and insulation properties but is now banned from use and persons involved in the handling of asbestos
materials installed in the past have to work in accordance with the regulation " The Control of Asbestos Regulations 2006".
Application of certain types of foam insulation in situ e.g. polyurethane
foam, requires careful handling of reactive ingredients and must do carried out in accordance with manufacturers instructions
and applicable regulations.
The notes below provide a basic outline of the principles involved in the provision of thermal insulation.
Notes:
Thermal Conductivity values (k-λ) for various materials are provide on webpage Thermal Conductivity coefficients
Thermal Conductivity values (k-λ) for various insulation materials are provide on this webpage Thermal Conductivity coefficients
Emissivity Values(e)for various material surfaces are provide on webpage Emissivity coefficients
Typical heat loss values for bare pipes, insulated pipes and plates are provided on webpage Heat loss tables
Symbols
A = Area of Surface (m 2 )
e = surface emissivity (dimensionless)
L = characteristic dimension (m)
Q = heat loss (W )
Q r = Radiated transferred energy (W)
Q co = Conducted transferred energy (W)
Q cv = Convective transferred energy (W)
q = heat loss per square metre of hot surface
(W/m2)
q 1 = heat loss per linear metre of pipe (W/ m)
R = thermal resistance of insulation per
(K/ W)
R 1 = thermal resistance of inner layer of insulation
(K/ W)
R 2 = thermal resistance of second layer of insulation
(K/ W)
R n = thermal resistance of nth layer of insulation
(K/ W)
R S = thermal resistance of outer surface of insulation
(K/ W)
T 1 = Temperature (Abs) of hot surface (oK)
T 2 = Temperature (Abs) of outer surface of insulation (oK)
T f = Temperature of hot fluid (oK)
T m = Temperature of ambient still air (oK)
T s = Temperature (Abs) of surface (oK)
|
d o = Outside diameter of pipe (m)
d 1 = outside diameter of inner layer of insulation
(mm)
d 2 = outside diameter of next layer of insulation
(m)
d n = outside diameter of nth layer of insulation
(m)
k (or λ ) = thermal conductivity of insulating material
(W/ mK)
k I = thermal conductivity of inner layer of
insulation (W/ mK)
k 2 = thermal conductivity of second layer of
insulation (W/ mK)
k n = thermal conductivity of nth layer of insulation
(W/ mK)
h = surface coefficient (W/m2 K).. (symbol f is also used for this variable)
h a = surface coefficient of inner surface (W/m2 K)
h b = surface coefficient of outer surface (W/m2 K)
h r = radiation surface heat transfer coefficient (W/m2 K)
h c = convection heat transfer coefficient (W/m2 K)
ln = natural logarithm
U = Overall Heat Transfer Coefficient,W m -2K -1
α = Stefan Boltzman constant = 5,673 x 10-8 W m-2 K-4
θ = Temperature difference (T 1 - T 2) (K)
|
Standards and Regulations
Building Regulations 2000
BS EN ISO 6946: 1997 Building components and
building elements - Thermal resistance and thermal transmittance
- Calculation method.
BS 5422:2001 Methods for specifying thermal insulating materials for pipes, tanks, vessels ductwork and equipment operating within temperature range of -40o C and 700o for
BS EN 823:1995 :Thermal insulating products for building applications. Determination of thickness
BS 3958-2:1982 :Thermal insulating materials. Calcium silicate preformed insulation
BS 3533:1981 :Glossary of thermal insulation terms
BS 4508-1:1986 : Thermally insulated underground pipelines. Specification for steel cased systems with air gap
BS 874-1:1986 :Methods for determining thermal insulating properties. Introduction, definitions and principles of measurement
BS EN ISO 9251:1996, ISO 9251:1987 :Thermal insulation. Heat transfer. Conditions and properties of materials. Vocabulary
BS EN ISO 9288:1996 :Thermal insulation. Heat transfer by radiation. Physical quantities and definitions
BS EN ISO 13787:2003 :Thermal insulation products for building equipment and industrial installations. Determination of declared thermal conductivity
BS EN ISO 8497:1997 :Thermal insulation. Determination of steady-state thermal transmission properties of thermal insulation for circular pipes
BS EN ISO 12241:1998:Thermal insulation for building equipment and industrial installations. Calculation rules
Calculations
Note: The following formulea relate to heat transfer conditions with air being the
relevant fluid surrounding the components under analysis and the heat transfer being by conduction, radiation, and Free convection..More general formulea are provided on webpage Heat Transfer
The insulation properties of insulation is basically identified by calculating
the reduction in heat transfer to the environment which is related to the heat transfer coefficient U.
heat tranfer Q = U A (T 1 - T 2)
Now UA is the reciprocal of the sum of thermal resistances of the heat transfer components in series and be expressed as
UA = 1 / ( R i + R 1 + R 2 + R 3....+ R o)
Now R iis the thermal resistance of the inner surface and R o is the thermal resistance of the outer surface (resulting from convection and radiation)
and R 1 , R 2 , R 3 etc are the thermal resistances of the various heat transfer component in series
The heat transfer is by conduction , radiation, and convection and the relevant formulea as applicable to
normal insulation systems are provided below.
Radiation
The heat transfer resulting from radiation for both plane and cylindrical
surfaces can be estimated using the formula
Q = α. e . A.(T 1 4 - T 2 4 ) = 5.673 x 10-8 e . A.(T 1 4 - T 2 4 )
α = Stefan Boltzman constant = 5,673 x 10-8 W m-2 K-4,
e = emissivity -see table for values (ref webpage Emissivity coefficients ) A = Surface Area
Now the heat transfer using the heat transfer coefficient =
Q r = h r A ( T 1 - T 2 )
therefore h r = α e 1 (T 1 + T 2 ) ( T 12 + T 22 )
Free Convection
The natural convection in free air under normal ambient conditions can be
estimated using the equation
Plane Surfaces
Q cv = C .A.(T s - T m ) n
Surface-direction | c | n |
Horizontal downward | 1,3 | 1,25 |
Vertical | 1,9 | 1,25 |
Horizontal upward | 2,5 | 1,25 |
Cylindrical Surfaces
An approximate evaluation of the heat loss results from using the equation..
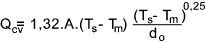
Conduction. (heat transfer through insulated systems
Note: The surface heat transfer coefficents h a and h b include radiation and convection components.
Single Layer
For Plane surfaces
The heat transfer through a single layer of insulation is provided by the equation
For an annular Cylinder
Inside diameter = d 1 outside diameter = d 2

Single Layer including surface losses
For Plane surfaces
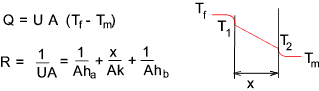
For an annular Cylinder
Inside diameter = d 1 outside diameter = d 2
Multi- Layer including surface losses
Plane surfaces
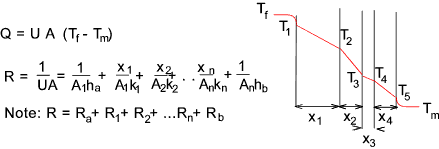
For a multi-layer annular cylinder
Inside diameter = d 1 outside diameter = d n
Surface coefficient
Approximate surface heat transfer coefficients that are reasonable accurate for low temperature
surfaces in still air ( which are the conditions experienced for insulated systems are listed below
h = 5,7 for low emissivity surfaces such as polished aluminium
h = 8,0 for surfaces of medium emissivity - galvanised steel , aluminium paint, stainless steel etc
h = 10 for surfaces of high emissivity - matt black surfaces, brick and plain insulated surfaces.
Physical Forms
Thermal insulation can be provided and installed in various physical forms
and using various methods as desicribed below
Slab or Board
Insulation can be supplied as rectangular shapes with uniform thickness for
covering flat surfaces walls, floors, ceilings etc. The slabs can be supplied in a range of
sizes but 600mm x 1200mm plan sizes are typical. These panels can be rigid or flexible depending
on the insulation material.
Pipe Sections
Insulation can be rolled or moulded as annular cylinders for the insulation of pipes
or small diameter vessels. The cylinders are normally supplied as segments.(2 ,3 or 4
segments making up a complete cylinder). Sizes can be supplied as standard for pipes
up to 1100mm dia.
Loose fill
Granular insulation can be supplied for packing, injecting, or pouring into irregular shaped
voids..A typical application for this form of insulation is cavity wall insulation.
Matts
Flexible /fibrous insulation can be supplied in rolls for wrapping around
or laying on surfaces. Flexible foam, mineral and natural wool, and glass fibre are used to
make up matts. The most well known typical application for this type of insulation
is for domestic loft insulation..
Sprayed insulation
Insulation which is mixed dry in the factory with inorganic fillers and binders
for application by wet spraying. This type of insulation is often based on mineral wool or
vermiculate.
Sprayed foam
Generally based on urethane with final chemical components mixed within
the spraying device.
Moulded Insulation products
Insulation which is poured as a slurry into a mould resulting in complex
shapes which are required for insulating such pipeline components as bends, flange covers
and valves.
Surface finishing of Insulation
Insulation as installed in voids and roof spaces is generally not provide with any
surface covering materials. However insulation over piping, equipment and
vessels is always covered for the following reasons.
1) Mechanical protection
2) To prevent dispersal of insulation material to environment
3) To improve the thermal characteristics of the insulation (Shiny aluminium sheets have low emissivity values
4) To improve the appearance of the insulated installation
Typical covering materials include
1) Aluminium foil- with bright polished outer surface
2) PVC - Providing attractive facings to tiles and reducing moisture absorption
3) Glass fibre cloth- Used for decorative purposes, providing mechanical strength and fire resistance
4) Wire netting is often used for wool type insulation provided enhanced mechanical strength and durability
Insulating Materials
The main requirement of an insulating material is that is shall have low
thermal conductivity. This is generally an intrinsic property of the insulating material but the structure of
the material may also make an important contribution to the insulating effect. If the material is porous,
conduction through it is partly through the air contained in the small pores, which are so
small that convection is minimised, and the heat transfer through the air is primarily by conduction. As gases (excluding hydrogen) are
the worst conductors of heat the air contained in the pores contributes significantly to the already poor
conduction properties of the material.
Aluminium Foil
The most frequently used metallic insulator. The insulation consists
of layers of reflective foil, each layer is crimped or corrugated. The directions of
the corrugations of adjacent layers being at right angles. Although aluminium is a very good
conductor the insulation properties result from the low emissivity of the shiny surfaces combined with the low conductivity
of the air contained in the voids separated by air insulation. The
effectiveness is related to the number of reflective sheets layers used.
This material is light and is used in refrigerating plant and for steam transfer pipes .
The effectiveness of aluminium is reduced if the reflective surfaces become dull . It
has low mechanical strength it is easily crushed or torn. It is therefore generally
provided with strong mechanical protective shells.
Rock wool
Rock wool is made from basalt or dolomite rocks. The
crushed rock, together with limestone and coke, is loaded
into a furnace where, it is melted at high temperatures of about 150OoC.
The molten rock directed into sets of rotating discs
which sling the melt off as fibres.
Resin binders, water
repellents and mineral oil are sprayed onto the fibres
as they leave the discs and fall under suction onto the
forming conveyor. From this stage the wool follows a
similar processing sequence to glass wool.
Rock wool is manufactured in rigid forms for use at temperatures up to 600oC in shapes including pipe sections
to suit pipes up to 600mm diameter. When used for pipes above 600mm dia
then bevelled slats are used.
The material is also used in flexible form for temperatures of up to 750oC.
Plastic compositions reinforced with non-asbestos fibres are also provided for easy application to
pipework. These are suitable for temperatures up to 100OoC
Ceramic
The different types of ceramic
materials made from a combination
of alumina, silica and china clay which are made by
blowing or extruding the liquid melt.
The resulting material is non-combustible , durable and strong which is
used as an insulating material and also can be used as a refractory
lining material. It is non-toxic and asbestos free and is used
in many forms. It can be applied by a spray and in loose form and in blanket
form.
It can be used at temperatures up to 160OoC is frost resistant and
has excellent resistance to chemical attack. The thickness can be increased
by spray build up and it adheres well to polished metals , glass etc.
Diatomaceous Earth (Kieselguhr, diamotite , fossil meal )
Found in natural state and dried resulting in structure similar
to magnesia but having a higher thermal conductivity. It has a low mechanical
strength and is therefore made up with fibres and clays. It can be used up to a maximum
temperature of 850oC in plastic form and 100OoC in rigid form
Magnesia
Magnesium carbonate is produced by extraction from dolomite rock,
which is then mixed with fibre reinforcement (generally about 15% fibres) and is
cast into appropriate moulds as slurry. After drying, the products are
machined to size. Product can also be supplied in plastic form (plasticized by water).
This material has a temperature range of 16oC to 315oC
Calcium silicate
A fibre reinforced compound of lime and silica with. It is
cast as a slurry into moulds which are process in autoclaves. The moulded products are then
machined to final size.
In the chemical industry, one of the most common insulation materials is calcium silicate. Calcium silicate is generally more appropriate for temperatures above 225 oC ,
while glass fibre is generally used at temperatures below 225 o C.
Exfoliated vermiculite
Vermiculite is a naturally occurring group of hydrated
aluminium/iron/magnesium silicates with a laminate
structure. The raw material is pulverised and is then subjected to direct
heat in a furnace, material 'exfoliates' or expands in size, into a form
consisting o of a series of parallel wafers with air spaces between.
Exfoliated vermiculite is produced as a granular loose fill which can
be bonded to form boards or dry mixed with fillers and
binders for spray application.
This material can be used at for temperatures up to 1100 o C.
Cellular glass
Powdered inorganic glass and crushed carbon are placed in moulds
and heated to 100OoC, at which temperature the carbon is
oxidized, forming gas bubbles which causes expansion of
the glass mix. This product can be cast into preformed pipe sections and
shapes with a density of about 155 kg/m3. The cellular material
is then annealed and, after cooling, if necessary cut to size. This material
has a wide temperature range of - 24OoC to 450oC
Glass wool
Glass wool is made from borosilicate glass whose principal
constituents are sand, soda ash dolomite, limestone, ulexite
and anhydrite.The constituents are melted in a furnace at about
140OoC and then the glass is directed into into spinners. These
rapidly rotating spinners have several thousand small holes
around the perimeter through which the glass is forced by
centrifugal force to form glass fibres. The fibres are sprayed
with resinous binders,water repellents and mineral oils as appropriate
and move through a suction area .
The treated fibres can then be formed into lightweight mats
flexible and semi-rigid, rigid slab, pipe sections, loose
wool, blowing wool, moulded products and mattresses.
Rigid polyurethane foam
Polyurethanes are manufactured by the mixing of various
resins, diisocyanates and catalysts producing an exothermic
reaction liberating the foaming agent and causes the
mix to expand. They are made in block moulds as
a batch process or are continuously foamed onto a paper or PVC substrate on a conveyor
system.
The material can also be dispensed in liquid form which is then formed in-situ
as a rigid foam and in this form is used increasingly for cavity wall insulation and
for pipe insulation by filling the annulus in jacketed pipes. It is particularly useful for
buried pipes which require insulation , strength and durability.
The polyisocyanurate type of urethane foam insulation is manufactured for use in high
flame risk areas and can be used at temperatures up to 130oC which is about
20oC higher than other urethane types.
Expanded polystyrene
Expandable polystyrene grains are heated by
steam, which causes them to expand. They are then
conditioned and, as they cool, the steam in the voids
within the beads condenses, thus permitting air to diffuse
into them. After conditioning, the granules can be cast into moulds
and further expanded using blown steam The
granules tend to fuse together, forming a rigid blocks. The
blocks are generally then later cut to shape.
This material has similar characteristics to poyurethane with excellent resistance
to moisture and with a high compressive strength. The applicable temperature
range is - 24OoC to 80oC
Extruded polystyrene
This is produced by a continuous extrusion process based on the steam injection
process. This results in a continuous product with a smooth-surface skin and
enhances the mechanical properties.
Polyisocyanurate foam
Polyisocyanurates are manufactured in a similar way to
polyurethanes, the chemical components being selected to
enhance their fire-safety properties.
Expanded perlite
Perlite is a naturally occurring sileceous rock. When
heated to over 100O0C the Perlite ore particles expand
to between 4 and 20 times their original volume.
The main form of supply is as a granular loose fill. When treated
the material in powder form can be used as a cavity fill or loft
insulation. It is also used as a filler in the production of lightweight
concrete and plasters.
Natural Insulation Materials
Natural insulation - overview
Natural insulation products have many properties that set them apart from
conventional materials. Overall, their impact on the environment
is much less than that of conventional insulation products.
Natural insulation materials are generally used in the builidng industry and
provide unique advantages..Their impact on the environment is less than with other insulation products.
The are made from animal or plant sources which are renewable. They are safe for installers and pleasant
to handle. They are reusable or biodegradable.
Most natural insulations materials are breathable i.e. they absorb moisture
in periods of high humidity and release it when the conditions are dry.
This reduces the risk of condensation and moisture therefore protecting the timber.
Note: If forests are being depleted for the production of newsprint and (cellulose ) insulation then it is not strictly correct
to apply the term renewable ref link the EURIMA download in links below...
Flax
Flax is a naturally occurring plant grown widely in
Europe. The flax fibres are interwoven and bound with
polyester fibres to form batts. This material is also supplied as mats. Borax is added to give protection
from fire and insect attack.
The density of flax use for insulation is such that there should be no interchange
between the enclosed and the outside air. A batt density of of between 45kg/m3 and
100 kg/m3 is acceptable.
Flax can be used for temperatures up to 320 oC
Cork
Cork is a product of the bark of the cork oak tree,
which grows in the Mediterranean area.
The bark is granulated and then steam baked in
moulds.
Cork is natural product with a temperature range of -16OoC to
90oC. It has a fair mechanical strength with good moisture resistance.
It is available in moulded sections and shapes and is easily formed. It has excellent
vibration resistance but poor fire resistance.
Cellulose
Cellulose insulation is manufactured from recycled newspaper
and magazines. The newspaper is shredded and
Boron salts are added to provide protection against fire,
vermin and organic growth.
Cellulose fibre can be used as loft insulation and cavity wall insulation
and for insulating timber frame walls, where
it will remain dry. It can be blown in dry or wet
sprayed.
This is a low cost insulation option for domestic loft and cavity wall insulation.
It is non-toxic and non-irritant, requiring no special clothing to handle it.
It is resistant to biological and fungal attack, treated against insects and unattractive
to vermin.
Cellulose is extremely fire resistant due with the addition of simple organic
salts and meets fire protection standards including BS 5803 Part 4.
Note: the information above is extracted from suppliers web site. Users are advised to consult
independent information sources when selecting this material -refer to EURIMA download below.
Sheep's wool
With the fall in the use of wool for clothing, there is a
growing interest in using it for building insulation. Wool
fibres are carded and aligned and bound with coir and polyester fibre.
Difficult to state limiting temperatures which may depend on how it is constructed
for particular uses.(it has an ignition temperature of about 560 oC
Wool is a natural fibre derived from a fully renewable resource.
Its ability to rapidly absorb water (improving with winter insulation) and release water
vapour(helping cooling in summer), with no loss of efficiency, makes Wool a
particularly effective thermal insulation material. This type of insulation can
retain its mechanical and thermal properties for 50 years.
Wool has a higher fire resistance than cellulose and cellular plastic insulants - it
does not burn but rather melts away from an ignition source and extinguishes itself.
It is however generally
treated to improve its fire resistance.
This material is generally used for roof insulation and cavity wall insulation.
Table Comparing Insulation Properties
Material |
Temperature Range |
Resistance to |
Forms |
Moisture |
Fire |
Mechanical |
Rigid |
Plastic |
Loose |
Flexible |
|
deg. C |
|
|
|
|
|
|
|
Glass Fibre |
-185 to 540 |
Excellent |
Excellent |
Poor |
Yes |
- |
Yes |
Mat |
Rock Wool |
up to 600 rigid to 750 flex |
Good |
Excellent |
Fair |
Yes |
Yes |
|
Mat |
Ceramic |
1600 |
Moderate |
Excellent |
Fair |
Yes |
Sprayed |
Yes |
Mat |
|
Calcium Silicate |
200 to 1000 |
Good |
Good |
Fair |
Yes |
- |
- |
- |
Magnesia |
up to 315 |
Poor |
Fair |
Poor |
Yes |
Yes |
- |
- |
Diatomaceous Earth |
850 to 1000 |
Poor |
Fair |
Poor |
Yes |
Yes |
Yes |
- |
Exfoliated vermiculite |
to 1100 |
Good |
Good |
Good |
Yes |
Sprayed Dispensed |
Yes |
- |
|
Foamed Glass |
-240 to 425 |
Excellent |
Excellent |
Good |
Yes |
- |
- |
- |
Polyurethane |
-240 to 110 |
Good |
Good |
Fair |
Yes |
Sprayed Dispensed |
- |
- |
Isocyanurate Foam |
-240 to110 |
Good |
Good |
Fair |
Yes |
Sprayed Dispensed |
- |
- |
Polystyrene |
-240 to 75 |
Good |
Good |
Fair |
Yes |
Sprayed Dispensed |
- |
- |
|
Cork |
-155 to 90 |
Good |
Fair |
Fair |
Yes |
- |
Yes |
- |
Flax |
up to 320 |
Good |
Fair |
- |
Yes |
- |
- |
- |
Cellulose |
|
Good |
Fair |
Fair |
Yes |
Yes |
- |
- |
Wool |
up to 250 |
Good |
Fair |
- |
- |
- |
Yes |
Yes |
|
Aluminium foil |
up to 600 |
Excellent |
Excellent |
Poor |
- |
- |
|
Yes |
Table of thermal conductivity values (k or λ )
Notes:
The values below are approximate. The thermal conductivity of a mateial is not
a static property and can vary with the temperature, density, and type and quantity of gas trapped inside
the pores or matrix...
This website currently uses k as the symbol for thermal conductivity. The modern
European trend has been to use the symbol λ. I may replace the k symbol at a later time
Insulation |
k (λ) =Wm-1K-1 |
|
Insulation |
k (λ) =Wm-1K-1 |
Balsa |
0,048 |
Straw-Comp |
0,09 |
Cotton Wool |
0,029 |
Polystyrene-Exp'd |
0,03 |
Felt |
0.04 |
Kapok |
0,034 |
Glass Wool (20o C ) |
0,04 |
Glass Wool (100oC) |
0,07 |
Magnesia |
0,07 |
Plywood |
0,13 |
Rock Wool |
0,045 |
Sawdust |
0,06 |
Slag Wool |
0,042 |
Wood |
0,13 |
Sheeps Wool |
0,038 |
Cellulose |
0,039 |
Expanded Perlite |
0,035 to 0,06 |
Polyisocyanurate foam |
0,023 |
Calcium silicate |
0.054-0.068 ( 100oC. ) |
Exfoliated vermiculite |
0.062 |
Cellular Glass |
0.043-0.055 |
Magnesia |
0.058 |
|