The notes below relate to spur gears.
Notes specific to helical gears are included on a separate page Helical Gears
Introduction
Gears are machine elements used to transmit rotary motion between two shafts, normally with
a constant ratio. The pinion is the smallest gear and the larger gear is called the gear wheel..
A rack is a rectangular prism with gear teeth machined along one side- it is in effect a gear wheel
with an infinite pitch circle diameter. In practice the action of gears in transmitting motion is a cam action each pair of mating teeth
acting as cams. Gear design has evolved to such a level that throughout the motion
of each contacting pair of teeth the velocity ratio of the gears is maintained fixed and the velocity
ratio is still fixed as each subsequent pair of teeth come into contact.
When the teeth action is such that the driving tooth moving at constant angular velocity produces
a proportional constant velocity of the driven tooth the action is termed a conjugate action. The teeth
shape universally selected for the gear teeth is the involute profile.
Consider one end of a piece of string is fastened to the OD of one cylinder and the other end of
the string is fastened to the OD of another cylinder parallel to the first and both cylinders
are rotated in the opposite directions to tension the string(see figure below). The point
on the string midway between the cylinder P is marked. As the left hand cylinder
rotates CCW the point moves towards this cylinder as it wraps on . The point moves away from the
right hand cylinder as the string unwraps. The point traces the involute form of the gear
teeth.
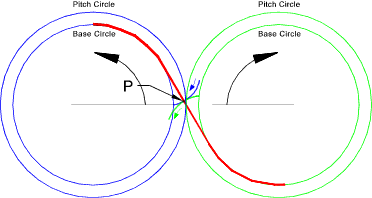
The lines normal to the point of contact of the gears always intersects the centre line joining the gear
centres at one point called the pitch point. For each gear the circle passing through
the pitch point is called the pitch circle. The gear ratio is proportional to the diameters
of the two pitch circles. For metric gears (as adopted by most of the worlds
nations) the gear proportions are based on the module.
m = (Pitch Circle Diameter(mm)) / (Number of teeth on gear).
In the USA the module is not used and instead
the Diametric Pitch d pis used d p = (Number of Teeth) / Diametrical Pitch (inches)
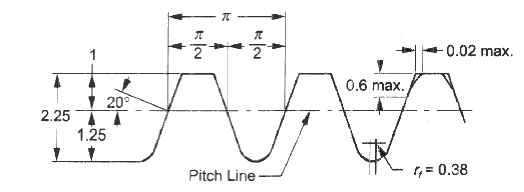 Profile of a standard
1mm module gear teeth for a gear with Infinite radius (Rack ). Other module teeth profiles
are directly proportion . e.g. 2mm module teeth are 2 x this profile
Many gears trains are very low power applications with an object of transmitting motion with minium
torque e.g. watch and clock mechanisms, instruments, toys, music boxes etc. These applications
do not require detailed strength calculations.
Standards
- AGMA 2001-C95 or AGMA-2101-C95 Fundamental Rating factors and Calculation Methods
for involute Spur Gear and Helical Gear Teeth
- BS 436-4:1996, ISO 1328-1:1995..Spur and helical gears. Definitions and allowable values of deviations relevant to corresponding flanks of gear teeth
- BS 436-5:1997, ISO 1328-2:1997..Spur and helical gears. Definitions and allowable values of deviations relevant to radial composite deviations and runout information
- BS ISO 6336-1:1996 ..Calculation of load capacity of spur and helical gears. Basic principles, introduction and general influence factors
- BS ISO 6336-2:1996..Calculation of load capacity of spur and helical gears. Calculation of surface durability (pitting)
- BS ISO 6336-3:1996..Calculation of load capacity of spur and helical gears. Calculation of tooth bending strength
- BS ISO 6336-5:2003..Calculation of load capacity of spur and helical gears. Strength and quality of materials
|
If it is necessary to design a gearbox from scratch the design process in selecting the
gear size is not complicated - the various design formulea have all been developed over time and are available in the
relevant standards. However significant effort, judgement and expertise is required in designing the whole
system including the gears, shafts , bearings, gearbox, lubrication. For the same
duty many different gear options are available for the type of gear , the materials and the
quality. It is always preferable to procure gearboxes from specialised gearbox manufacturers
Terminology - spur gears
- Diametral pitch (d p )...... The number of teeth per one inch of pitch circle diameter.
- Module. (m) ...... The length, in mm, of the pitch circle diameter per tooth.
- Circular pitch (p)...... The distance between adjacent teeth measured along the are at the
pitch circle diameter
- Addendum ( h a )...... The height of the tooth above the pitch circle diameter.
- Centre distance (a)...... The distance between the axes of two gears in mesh.
- Circular tooth thickness (ctt)...... The width of a tooth measured along the are at the pitch circle diameter.
- Dedendum ( h f )...... The depth of the tooth below the pitch circle diameter.
- Outside diameter ( D o )...... The outside diameter of the gear.
- Base Circle diameter ( D b ) ...... The diameter on which the involute teeth profile is based.
- Pitch circle dia ( p ) ...... The diameter of the pitch circle.
- Pitch point...... The point at which the pitch circle diameters of two gears in mesh coincide.
- Pitch to back...... The distance on a rack between the pitch circle diameter line and
the rear face of the rack.
- Pressure angle ...... The angle between the tooth profile at the pitch circle diameter
and a radial line passing through the same point.
- Whole depth...... The total depth of the space between adjacent teeth.
|
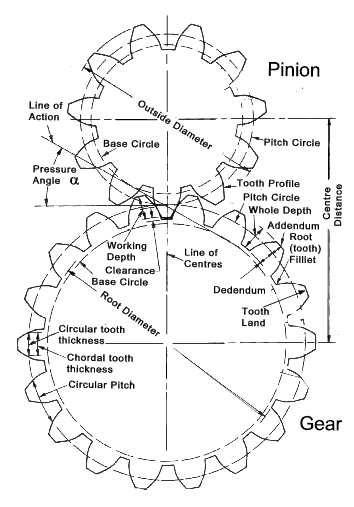
Spur Gear Design
The spur gear is is simplest type of gear manufactured and is generally used for transmission
of rotary motion between parallel shafts. The spur gear is the first choice option for gears except when high speeds, loads, and
ratios direct towards other options. Other gear types may also be preferred
to provide more silent low-vibration operation. A single spur gear is generally selected to have
a ratio range of between 1:1 and 1:6 with a pitch line velocity up to 25 m/s. The spur gear has an operating
efficiency of 98-99%. The pinion is made from a harder material than the wheel. A gear pair should
be selected to have the highest number of teeth consistent with a suitable safety margin in strength and wear.
The minimum number of teeth on a gear with a normal pressure angle of 20 desgrees is 18.
The preferred number of teeth are as follows
12 13 14 15 16 18 20 22 24 25 28 30 32 34 38 40 45 50 54 60 64 70 72 75 80 84 90 96 100 120 140 150 180 200 220 250 |
Materials used for gears
Mild steel is a poor material for gears as as it has poor resistance to surface
loading. The carbon content for unhardened gears is generally 0.4%(min) with 0.55%(min)
carbon for the pinions. Dissimilar materials should be used for the meshing gears - this particularly
applies to alloy steels. Alloy steels have superior fatigue properties compared to
carbon steels for comparable strengths. For extremely high gear loading case hardened
steels are used the surface hardening method employed should be such to provide sufficient case depth for the final grinding process used.
| |
Material | Notes | applications |
Ferrous metals |
Cast Iron | Low Cost easy to machine with high damping | Large moderate power, commercial gears |
Cast Steels | Low cost, reasonable strength | Power gears with medium rating to commercial quality |
Plain-Carbon Steels | Good machining, can be heat treated | Power gears with medium rating to commercial/medium quality |
Alloy Steels | Heat Treatable to provide highest strength and durability | Highest power requirement. For precision and high precisiont |
Stainless Steels (Aust) | Good corrosion resistance. Non-magnetic | Corrosion resistance with low power ratings. Up to precision quality |
Stainless Steels (Mart) | Hardenable, Reasonable corrosion resistance, magnetic | Low to medium power ratings Up to high precision levels of quality |
Non-Ferrous metals |
Aluminium alloys | Light weight, non-corrosive and good machinability | Light duty instrument gears up to high precision quality |
Brass alloys | Low cost, non-corrosive, excellent machinability | low cost commercial quality gears. Quality up to medium precision |
Bronze alloys | Excellent machinability, low friction and good compatability with steel | For use with steel power gears. Quality up to high precision |
Magnesium alloys | Light weight with poor corrosion resistance | Ligh weight low load gears. Quality up to medium precision |
Nickel alloys | Low coefficient of thermal expansion. Poor machinability | Special gears for thermal applications to commercial quality |
Titanium alloys | High strength, for low weight, good corrosion resistance | Special light weight high strength gears to medium precision |
Di-cast alloys | Low cost with low precision and strength | High production, low quality gears to commercial quality |
Sintered powder alloys | Low cost, low quality, moderate strength | High production, low quality to moderate commercial quality |
Non metals |
Acetal (Delrin | Wear resistant, low water absorbtion | Long life , low load bearings to commercial quality |
Phenolic laminates | Low cost, low quality, moderate strength | High production, low quality to moderate commercial quality |
Nylons | No lubrication, no lubricant, absorbs water | Long life at low loads to commercial quality |
PTFE | Low friction and no lubrication | Special low friction gears to commercial quality |
Equations for basic gear relationships
It is acceptable to marginally modify these relationships e.g to modify the addendum /dedendum to
allow Centre Distance adjustments. Any changes modifications will affect the gear performance
in good and bad ways...
Addendum | h a = m = 0.3183 p |
Base Circle diameter | Db = d.cos α |
Centre distance | a = ( d g + d p) / 2 |
Circular pitch | p = m.π |
Circular tooth thickness | ctt = p/2 |
Dedendum | h f = h - a = 1,25m = 0,3979 p |
Module | m = d /z |
Number of teeth | z = d / m |
Outside diameter | D o = (z + 2) x m |
Pitch circle diameter | d = z . m ... (d g = gear & d p = pinion ) |
Whole depth(min) | h = 2.25 . m |
Top land width(min) | t o = 0,25 . m |
Module (m)
The module is the ratio of the pitch diameter to the number of teeth. The unit of the module
is milli-metres.Below is a diagram showing the relative size of teeth machined in a rack with module ranging
from module values of 0,5 mm to 6 mm

The preferred module values are
0,5 0,8 1
1,25
1,5 2,5 3
4 5 6
8 10 12
16 20 25
32 40 50
Normal Pressure angle α
An important variable affecting the geometry of the gear teeth is the normal pressure
angle. This is generally standardised at 20o. Other pressure
angles should be used only for special reasons and using considered judgment.
The following changes result from increasing the pressure angle
- Reduction in the danger of undercutting and interference
- Reduction of slipping speeds
- Increased loading capacity in contact, seizure and wear
- Increased rigidity of the toothing
- Increased noise and radial forces
|
Gears required to have low noise levels have pressure angles 15o to17.5o
Contact Ratio
The gear design is such that when in mesh the rotating gears have more than one gear
in contact and transferring the torque for some of the time. This property is called
the contact ratio. This is a ratio of the length of the line-of-action to the base pitch.
The higher the contact ratio the more the load is shared between teeth. It is good practice to maintain a contact ratio of 1.2 or greater.
Under no circumstances should the ratio drop below 1.1.
A contact ratio between 1 and 2 means that part of the time two pairs of teeth are
in contact and during the remaining time one pair is in contact. A ratio
between 2 and 3 means 2 or 3 pairs of teeth are always in contact.
Such as high contact ratio generally is not obtained with external spur gears, but
can be developed in the meshing of an internal and external spur gear pair or
specially designed non-standard external spur gears.
(Rgo2 - Rgb2 )1/2 + (Rpo2 - Rpb2 )1/2 - a sin α
contact ratio m =
p cos α
R go = D go / 2..Radius of Outside Dia of Gear
R gb = D gb / 2..Radius of Base Dia of Gear
R po = D po / 2..Radius of Outside Dia of Pinion
R pb = D pb / 2..Radius of Base Dia of Pinion
p = circular pitch.
a = ( d g+ d p )/2 = center distance.
Spur gear Forces, torques, velocities & Powers
- F = tooth force between contacting teeth (at angle pressure angle α to pitch line tangent. (N)
- F t = tangential component of tooth force (N)
- F s = Separating component of tooth force
- α= Pressure angle
- d 1 = Pitch Circle Dia -driving gear (m)
- d 2 = Pitch Circle Dia -driven gear (m)
- ω 1 = Angular velocity of driver gear (Rads/s)
- ω 2 = Angular velocity of driven gear (Rads/s)
- z 1 = Number of teeth on driver gear
- z 2 = Number of teeth on driven gear
- P = power transmitted (Watts)
- M = torque (Nm)
- η = efficiency
|
Tangential force on gears F t = F cos α
|
Separating force on gears F s = F t tan α
|
Torque on driver gear T 1 = F t d 1 / 2
|
Torque on driver gear T 2 = F t d 2 / 2
|
Speed Ratio =ω 1 / ω 2 = d 2 / d 1 = z 2 /z 1
|
Input Power P 1 = T1 .ω 1
|
Output Power P 2 =η.T 1 .ω 2
|
Spur gear Strength and durability calculations
Designing spur gears is normally done in accordance with standards the two most
popular series are listed under standards above:
The notes below relate to approximate methods for estimating gear strengths. The methods are really only
useful for first approximations and/or selection of stock gears (ref links below). Detailed design of spur and helical
gears is best completed using the standards. Books are available providing the
necessary guidance. Software is also available making the process very easy.
A very reasonably priced and easy to use package is included in the links below (Mitcalc.com)
The determination of the capacity of gears to transfer the required torque for the
desired operating life is completed by determining the strength of the gear teeth in
bending and also the durability i.e of the teeth ( resistance to wearing/bearing/scuffing loads ) .. The equations below are based on methods
used by Buckingham..
Bending
The basic bending stress for gear teeth is obtained by using the Lewis formula
σ = Ft / ( ba. m. Y )
|
- F t = Tangential force on tooth
- σ = Tooth Bending stress (MPa)
- b a = Face width (mm)
- Y = Lewis Form Factor
- m = Module (mm)
Note: The Lewis formula is often expressed as
σ = Ft / ( ba. p. y )
Where y = Y/π and p = circular pitch
When a gear wheel is rotating the gear teeth come into contact with some degree
of impact. To allow for this a velocity factor ( Kv ) is introduced into the equation.
This is given by the Barth equation...
V = the pitch line velocity = d.ω/2 (m/s)
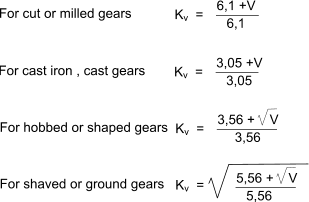
The Lewis formula is thus modified as follows
σ = K v.Ft / ( ba. m. Y )
Surface Durability
This calculation involves determining the contact stress between the gear teeth and utilises a Herzian contact stress analysis
. This is based on the analysis of two cylinders ,in contact alon their length and subject to a radial force.
σ w = 2.F / ( π .b .l )
σ w = largest surface pressure
F = force pressing the two cylinders (gears) together
l = length of the cylinders (gear)
b = halfwidth = half of the width of the contact surface between the two cylinders.
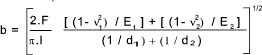
d 1 ,d 2 Are the diameters for the two contacting cylinders.
ν 1, ν 2 Poisson ratio for the two gear materials
E 1 ,E 2 Are the Young's Modulus Values for the two gears
To arrive at the formula used for gear calculations the following changes are made
σ w is replaced by σ c (dynamic contact stress)
F is replaced by F t / cos α
d is replaced by 2.r
l is replaced by W ( Face width of gear)
The velocity factor K v as described above is introduced.
Also an elastic constant Z E is created
When the value of E used is in MPa then the units of Ze are √ MPa . The Imperial version of Ze
is Cp with value of E used in psi and value of Cp = √ psi
The resulting formula for the compressive stress developed is as shown below
Note: r1 and r2are the radii of curvature of the tooth surfaces at the contact point.
As gear tooth wear is generally first found at the pitch point, the curvatures at the pitch point are used:
r1 = d1 sin α /2
r2 = d2 sin α /2
The dynamic contact stress σc developed by the transmitted torque
must be less than the allowable contact stress Se...
Note: Values for Allowable stress value (Se) and the elastic constant ZE for some materials
are provided at Gear Table
Important Note: The above equations do not take into account the various factors which are
integral to calculations completed using the relevant standards. These equations therefore
yield results suitable for first estimate design purposes only...
Design Process
To select gears from a stock gear catalogue or do a first approximation for a
gear design select the gear material and obtain a safe working stress e.g Yield stress / Factor of Safety. /Safe fatigue stress
- Determine the input speed, output speed, ratio, torque to be transmitted
- Select materials for the gears ( pinion is more highly loaded than gear )
- Determine safe working stresses (uts /factor of safety or yield stress/factor of safety or Fatigue strength / Factor of safety )
- Determine Allowable endurance Stress Se
- Select a module value and determine the resulting geometry of the gear
- Use the lewis formula and the endurance formula to establish the resulting face width
- If the gear proportions are reasonable then - proceed to more detailed evaluations
- If the resulting face width is excessive - change the module or material or both and start again
|
The gear face width should be selected in the range 9-15 x module or
for straight spur gears-up to 60% of the pinion diameter.
Internal Gears
Advantages:
- Geometry ideal for epicyclic gear design
- Allows compact design since the center distance is less than for external gears.
- A high contact ratio is possible.
- Good surface endurance due to a convex profile surface working against a concave surface.
|
Disadvantages:
- Housing and bearing supports are more complicated, because the external gear nests
within the internal gear.
- Low ratios are unsuitable and in many cases impossible because of interferences.
- Fabrication is limited to the shaper generating process, and usually special tooling is required.
|
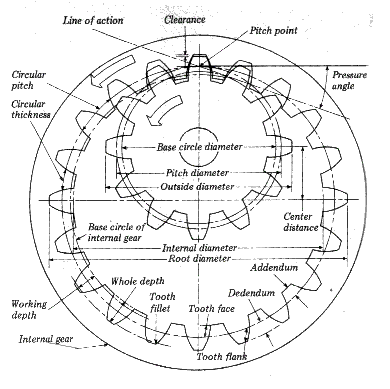
Lewis form factor.
Table of lewis form factors for different tooth forms and pressure angles
No Teeth |
|
Load Near Tip of Teeth |
Load at Near Middle of Teeth |
14 1/2 deg |
20 deg FD |
20 deg Stub |
25 deg |
14 1/2 deg |
20 deg FD |
|
|
Y |
y |
Y |
y |
Y |
y |
Y |
y |
Y |
y |
Y |
y |
10 |
|
0,176 |
0,056 |
0,201 |
0,064 |
0,261 |
0,083 |
0,238 |
0,076 |
|
|
|
|
11 |
|
0,192 |
0,061 |
0,226 |
0,072 |
0,289 |
0,092 |
0,259 |
0,082 |
|
|
|
|
12 |
|
0,21 |
0,067 |
0,245 |
0,078 |
0,311 |
0,099 |
0,277 |
0,088 |
0,355 |
0,113 |
0,415 |
0,132 |
13 |
|
0,223 |
0,071 |
0,264 |
0,084 |
0,324 |
0,103 |
0,293 |
0,093 |
0,377 |
0,12 |
0,443 |
0,141 |
14 |
|
0,236 |
0,075 |
0,276 |
0,088 |
0,339 |
0,108 |
0,307 |
0,098 |
0,399 |
0,127 |
0,468 |
0,149 |
15 |
|
0,245 |
0,078 |
0,289 |
0,092 |
0,349 |
0,111 |
0,32 |
0,102 |
0,415 |
0,132 |
0,49 |
0,156 |
16 |
|
0,255 |
0,081 |
0,295 |
0,094 |
0,36 |
0,115 |
0,332 |
0,106 |
0,43 |
0,137 |
0,503 |
0,16 |
17 |
|
0,264 |
0,084 |
0,302 |
0,096 |
0,368 |
0,117 |
0,342 |
0,109 |
0,446 |
0,142 |
0,512 |
0,163 |
18 |
|
0,27 |
0,086 |
0,308 |
0,098 |
0,377 |
0,12 |
0,352 |
0,112 |
0,459 |
0,146 |
0,522 |
0,166 |
19 |
|
0,277 |
0,088 |
0,314 |
0,1 |
0,386 |
0,123 |
0,361 |
0,115 |
0,471 |
0,15 |
0,534 |
0,17 |
20 |
|
0,283 |
0,09 |
0,32 |
0,102 |
0,393 |
0,125 |
0,369 |
0,117 |
0,481 |
0,153 |
0,544 |
0,173 |
21 |
|
0,289 |
0,092 |
0,326 |
0,104 |
0,399 |
0,127 |
0,377 |
0,12 |
0,49 |
0,156 |
0,553 |
0,176 |
22 |
|
0,292 |
0,093 |
0,33 |
0,105 |
0,404 |
0,129 |
0,384 |
0,122 |
0,496 |
0,158 |
0,559 |
0,178 |
23 |
|
0,296 |
0,094 |
0,333 |
0,106 |
0,408 |
0,13 |
0,390 |
0,124 |
0,502 |
0,16 |
0,565 |
0,18 |
24 |
|
0,302 |
0,096 |
0,337 |
0,107 |
0,411 |
0,131 |
0,396 |
0,126 |
0,509 |
0,162 |
0,572 |
0,182 |
25 |
|
0,305 |
0,097 |
0,34 |
0,108 |
0,416 |
0,132 |
0,402 |
0,128 |
0,515 |
0,164 |
0,58 |
0,185 |
26 |
|
0,308 |
0,098 |
0,344 |
0,109 |
0,421 |
0,134 |
0,407 |
0,13 |
0,522 |
0,166 |
0,584 |
0,186 |
27 |
|
0,311 |
0,099 |
0,348 |
0,111 |
0,426 |
0,136 |
0,412 |
0,131 |
0,528 |
0,168 |
0,588 |
0,187 |
28 |
|
0,314 |
0,1 |
0,352 |
0,112 |
0,43 |
0,137 |
0,417 |
0,133 |
0,534 |
0,17 |
0,592 |
0,188 |
29 |
|
0,316 |
0,101 |
0,355 |
0,113 |
0,434 |
0,138 |
0,421 |
0,134 |
0,537 |
0,171 |
0,599 |
0,191 |
30 |
|
0,318 |
0,101 |
0,358 |
0,114 |
0,437 |
0,139 |
0,425 |
0,135 |
0,54 |
0,172 |
0,606 |
0,193 |
31 |
|
0,32 |
0,101 |
0,361 |
0,115 |
0,44 |
0,14 |
0,429 |
0,137 |
0,554 |
0,176 |
0,611 |
0,194 |
32 |
|
0,322 |
0,101 |
0,364 |
0,116 |
0,443 |
0,141 |
0,433 |
0,138 |
0,547 |
0,174 |
0,617 |
0,196 |
33 |
|
0,324 |
0,103 |
0,367 |
0,117 |
0,445 |
0,142 |
0,436 |
0,139 |
0,55 |
0,175 |
0,623 |
0,198 |
34 |
|
0,326 |
0,104 |
0,371 |
0,118 |
0,447 |
0,142 |
0,44 |
0,14 |
0,553 |
0,176 |
0,628 |
0,2 |
35 |
|
0,327 |
0,104 |
0,373 |
0,119 |
0,449 |
0,143 |
0,443 |
0,141 |
0,556 |
0,177 |
0,633 |
0,201 |
36 |
|
0,329 |
0,105 |
0,377 |
0,12 |
0,451 |
0,144 |
0,446 |
0,142 |
0,559 |
0,178 |
0,639 |
0,203 |
37 |
|
0,33 |
0,105 |
0,38 |
0,121 |
0,454 |
0,145 |
0,449 |
0,143 |
0,563 |
0,179 |
0,645 |
0,205 |
38 |
|
0,333 |
0,106 |
0,384 |
0,122 |
0,455 |
0,145 |
0,452 |
0,144 |
0,565 |
0,18 |
0,65 |
0,207 |
39 |
|
0,335 |
0,107 |
0,386 |
0,123 |
0,457 |
0,145 |
0,454 |
0,145 |
0,568 |
0,181 |
0,655 |
0,208 |
40 |
|
0,336 |
0,107 |
0,389 |
0,124 |
0,459 |
0,146 |
0,457 |
0,145 |
0,57 |
0,181 |
0,659 |
0,21 |
43 |
|
0,339 |
0,108 |
0,397 |
0,126 |
0,467 |
0,149 |
0,464 |
0,148 |
0,574 |
0,183 |
0,668 |
0,213 |
45 |
|
0,34 |
0,108 |
0,399 |
0,127 |
0,468 |
0,149 |
0,468 |
0,149 |
0,579 |
0,184 |
0,678 |
0,216 |
50 |
|
0,346 |
0,11 |
0,408 |
0,13 |
0,474 |
0,151 |
0,477 |
0,152 |
0,588 |
0,187 |
0,694 |
0,221 |
55 |
|
0,352 |
0,112 |
0,415 |
0,132 |
0,48 |
0,153 |
0,484 |
0,154 |
0,596 |
0,19 |
0,704 |
0,224 |
60 |
|
0,355 |
0,113 |
0,421 |
0,134 |
0,484 |
0,154 |
0,491 |
0,156 |
0,603 |
0,192 |
0,713 |
0,227 |
65 |
|
0,358 |
0,114 |
0,425 |
0,135 |
0,488 |
0,155 |
0,496 |
0,158 |
0,607 |
0,193 |
0,721 |
0,23 |
70 |
|
0,36 |
0,115 |
0,429 |
0,137 |
0,493 |
0,157 |
0,501 |
0,159 |
0,61 |
0,194 |
0,728 |
0,232 |
75 |
|
0,361 |
0,115 |
0,433 |
0,138 |
0,496 |
0,158 |
0,506 |
0,161 |
0,613 |
0,195 |
0,735 |
0,234 |
80 |
|
0,363 |
0,116 |
0,436 |
0,139 |
0,499 |
0,159 |
0,509 |
0,162 |
0,615 |
0,196 |
0,739 |
0,235 |
90 |
|
0,366 |
0,117 |
0,442 |
0,141 |
0,503 |
0,16 |
0,516 |
0,164 |
0,619 |
0,197 |
0,747 |
0,238 |
100 |
|
0,368 |
0,117 |
0,446 |
0,142 |
0,506 |
0,161 |
0,521 |
0,166 |
0,622 |
0,198 |
0,755 |
0,24 |
150 |
|
0,375 |
0,119 |
0,458 |
0,146 |
0,518 |
0,165 |
0,537 |
0,171 |
0,635 |
0,202 |
0,778 |
0,248 |
200 |
|
0,378 |
0,12 |
0,463 |
0,147 |
0,524 |
0,167 |
0,545 |
0,173 |
0,64 |
0,204 |
0,787 |
0,251 |
300 |
|
0,38 |
0,122 |
0,471 |
0,15 |
0,534 |
0,17 |
0,554 |
0,176 |
0,65 |
0,207 |
0,801 |
0,255 |
Rack |
|
0,39 |
0,124 |
0,484 |
0,154 |
0,55 |
0,175 |
0,566 |
0,18 |
0,66 |
0,21 |
0,823 |
0,262 |
|